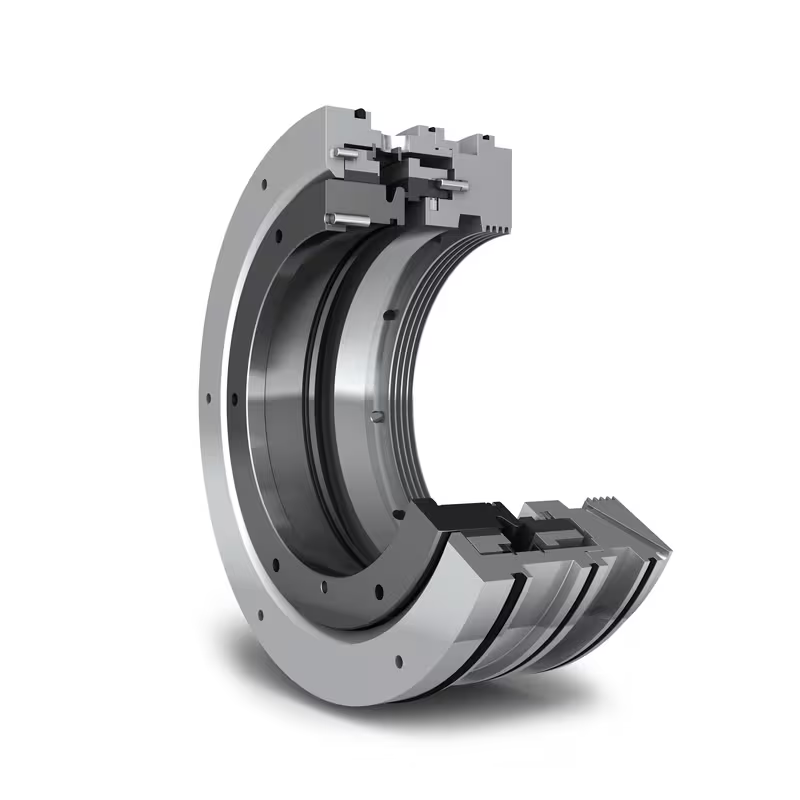
K-MOS Mechanical Oil Seal
The K-MOS operates by using oil at 30-45 psi above process gas pressure to contain process gas inside the equipment body. The mechanical seal faces work to minimize the amount of oil flowing to the sour drain pots. Leakage is collected in drain pots where it is either treated and re-used or discarded. Sour oil leakage is normally less than five gallons per day and less than one gallon per day during standby. If you are experiencing higher levels of oil consumption with your current mechanical seals, contact us to discuss solutions.
Features and Benefits
- Low sour oil leakage during operation
- Near zero standby leakage
- Pressure balanced face seal design minimizes friction wear
- Steel retainers for carbon sealing rings provide durability and stability to critical components
- Solid PTFE dynamic secondary seals reduce the possibility of seal “hang up”
- Integral process side windbacks direct leakage to drainers, and out of the process stream
- Rotating seal faces are hard-coated for longevity
- Generous axial float allowance
- Cartridge design for easy installation
- Typical seal run times of 5-8 years between overhaul
Applications
- Natural gas transmission
- Pipeline booster compressor shaft seals
- Natural gas and CO2 re-injection compressor shaft seals
- Natural gas processing plants
- Propane refrigeration, sales gas, raw gas, residue gas compressor shaft seals
- LNG refrigeration and boil-off compressor shaft seals
- Refinery
- Hydrogen recycle, platformer, reformer, wet gas, coker, alkylation, isomerization, flare gas recovery, crude unit
- Petrochemical
- Ethylene, propylene, polypropylene, charge gas, propane refrigeration, iso-butane, ethylene oxide, styrene off-gas, low density polyethylene (LDPE), linear low density polyethylene (LLDPE), polyethylene, carbon monoxide, methanol, synthesis gas, ammonia refrigeration, acetylene, feed gas